All About Sensor Liquid Level
Understanding How We Sensor Liquid Level the Smart Way!
Have you ever poured a drink and stopped before it spilled over the top? That’s kind of what a Sensor Liquid Level does—except it does it for machines and tanks, and it’s a lot smarter and faster!
In this guide, we’ll explore:
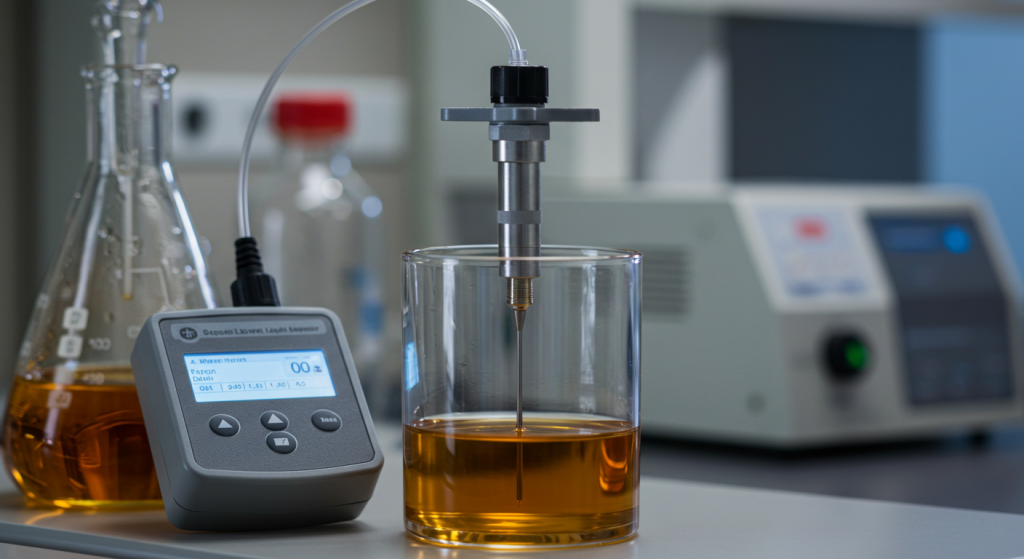
What is a Sensor Liquid Level System?
A sensor liquid level system is a technology designed to monitor and control the level of liquid in a tank or container. These systems are used in various industries like water treatment plants, chemical factories, agriculture, and even in homes for applications like rainwater harvesting or sump pumps. The core function of these systems is to ensure that the liquid level remains within a desired range, preventing overflow, underflow, or potential damage to equipment.
These systems consist of a sensor (or multiple sensors) that detects the level of liquid, sending this data to a control system that can activate pumps, valves, or alarms. By providing real-time information and control, sensor liquid level systems improve safety, efficacité, and reliability.
How Does a Sensor Liquid Level System Work?
A sensor liquid level system works by detecting the level of liquid in a tank and automatically adjusting the flow of liquid to maintain a desired level. Here’s how it works:
- Sensor Installation: The liquid level sensor is installed at a specific location in the tank or container. The sensor can be based on different technologies like ultrasonic, capacitive, or float-type sensors. Each sensor type has its unique method for measuring the liquid level.
- Detection of Liquid Level: Once installed, the sensor continuously monitors the liquid level in the tank. Depending on the type of sensor used:
- Float-based sensors: Use a floating object that rises and falls with the liquid level, triggering switches to indicate the liquid’s height.
- Capacitive sensors: Measure the change in capacitance as the liquid level changes.
- Ultrasonic sensors: Use sound waves to measure the distance between the sensor and the liquid’s surface.
- Signal Transmission: The sensor sends data to the controller, a central unit that processes the information. This could be a manual display, a smartphone app, or an automated control system.
- Control Mechanism: Based on the sensor’s data, the controller decides whether to activate or deactivate a pump, valve, or other devices. Par exemple:
- If the liquid level is too low, the controller could activate a pump to fill the tank.
- If the liquid level is too high, the system may close a valve or trigger an alarm to prevent overflow.
- Feedback and Adjustment: The system continues to monitor and make adjustments automatically, maintaining the liquid at a stable level without manual intervention.
Types of Liquid Level Sensors
Several types of sensors can be used to monitor liquid levels, each with specific advantages depending on the application. Some common types include:
Float-based Sensors
Float-based sensors use a buoyant object that floats on the surface of the liquid. As the liquid level rises or falls, the float moves up or down, activating mechanical or electronic switches that signal the system to take action.
- Advantages: Simple design, low cost, and easy to install.
- Disadvantages: Mechanical parts can wear out over time, and they may not be suitable for aggressive liquids or environments with turbulence.
Capacitive Sensors
Capacitive liquid level sensors work by measuring the change in capacitance between two electrodes as the liquid level changes. These sensors are non-contact and can measure the level without touching the liquid.
- Advantages: Accurate, no moving parts, and capable of detecting a wide range of liquids.
- Disadvantages: May be affected by temperature, pressure, or the type of liquid being measured.
Ultrasonic Sensors
Ultrasonic sensors measure the distance between the sensor and the surface of the liquid by emitting high-frequency sound waves and measuring the time it takes for the waves to reflect back.
- Advantages: Non-contact, suitable for a wide range of liquids, and able to measure through the tank’s surface material.
- Disadvantages: Sensitive to environmental factors like temperature, pressure, and vapor in the air.
Radar Sensors
Radar sensors use radio waves to measure the level of liquid in a tank. These sensors send out a signal that reflects off the liquid’s surface and returns to the sensor, providing the level data.
- Advantages: Very accurate, reliable, and unaffected by temperature, pressure, or vapor.
- Disadvantages: More expensive than other sensor types, and installation may be more complex.
Optical Sensors
Optical sensors use light to detect the liquid level. They can be configured with optical fibers to detect when the light is blocked by the presence of liquid.
- Advantages: High accuracy, simple design, and good for small containers.
- Disadvantages: May not be suitable for highly turbid or dirty liquids.
Applications of Sensor Liquid Level Systems
Sensor liquid level systems are used in various applications across many industries. Here are some examples:
Water and Wastewater Treatment
In water and wastewater treatment plants, sensor liquid level systems are used to monitor the levels of chemicals, eau, and other liquids in tanks. These systems help automate the process, ensuring that chemicals are added in the correct amounts and that tanks do not overflow.
Oil and Gas Industry
In the oil and gas industry, accurate measurement of liquid levels in storage tanks, pipelines, and reservoirs is critical. Liquid level sensors help monitor and control the flow of oil and gas, preventing overflows and ensuring efficient operations.
Agriculture and Irrigation
Farmers use liquid level sensors in irrigation systems to control the flow of water to crops. These sensors help ensure that crops receive just the right amount of water, preventing waste and improving efficiency in water use.
Fuel Storage and Distribution
In fuel storage tanks, liquid level sensors help monitor fuel levels to ensure safe and efficient storage. These sensors can trigger alarms if the tank is full or near empty, allowing for timely refills or avoiding overflows.
Chemical Processing
In chemical plants, liquid level sensors are used to monitor hazardous chemicals and liquids in tanks, ensuring that the chemicals are handled safely. These sensors also help prevent leaks and spills, reducing the risk of accidents.
Benefits of Using Sensor Liquid Level Systems
The integration of sensor liquid level systems brings many advantages to industries and households alike:
Prevention of Overflow and Spillage
One of the primary benefits of sensor liquid level systems is preventing overflow. By continuously monitoring the liquid level, these systems help ensure that tanks or containers do not exceed their maximum capacity, thus avoiding messy spills and potential damage to the surrounding area.
Cost Savings
By ensuring efficient use of liquids, sensor systems help reduce waste and overfilling, which can lead to costly losses. They also help automate processes, reducing the need for manual checks and labor costs.
Increased Safety
In industries dealing with hazardous materials or chemicals, sensor liquid level systems are critical for maintaining safety. These systems prevent overflows and spills that could result in dangerous situations, such as contamination or accidents.
Improved Efficiency
Sensor systems improve efficiency by providing real-time data on liquid levels. This data can be used to optimize processes, improve scheduling, and automate control systems. In industries like irrigation or manufacturing, this leads to better resource management and streamlined operations.
Remote Monitoring
Many modern liquid level sensors can be connected to remote monitoring systems, allowing operators to monitor and control liquid levels from a distance. This capability is especially useful for large facilities or operations spread out over a large area.
Conclusion
Sensor liquid level systems are an essential technology for industries and households that need to monitor and manage liquid levels accurately and efficiently. By providing real-time data and automatic control, these systems prevent costly spills, improve safety, save water, and increase operational efficiency.
Whether you’re using these systems in industrial applications or for home automation, sensor liquid level systems offer a reliable, cost-effective way to ensure that liquid levels are always within the desired range, reducing waste and improving overall system performance.