Industrial Water Level Sensor: A Complete In-Depth Guide for Beginners and Students
Industrial water level sensor is one of the most important resources in the world, not just for people at home, but for industries too. Factories, farms, power plants, and water treatment facilities use water every day for many different purposes. But using water the right way means knowing exactly how much water is available. That’s why industries rely on industrial water level sensors. These tools measure and monitor how much water is in large tanks, pipelines, or systems, helping workers control water use, avoid overflows, and prevent running dry.
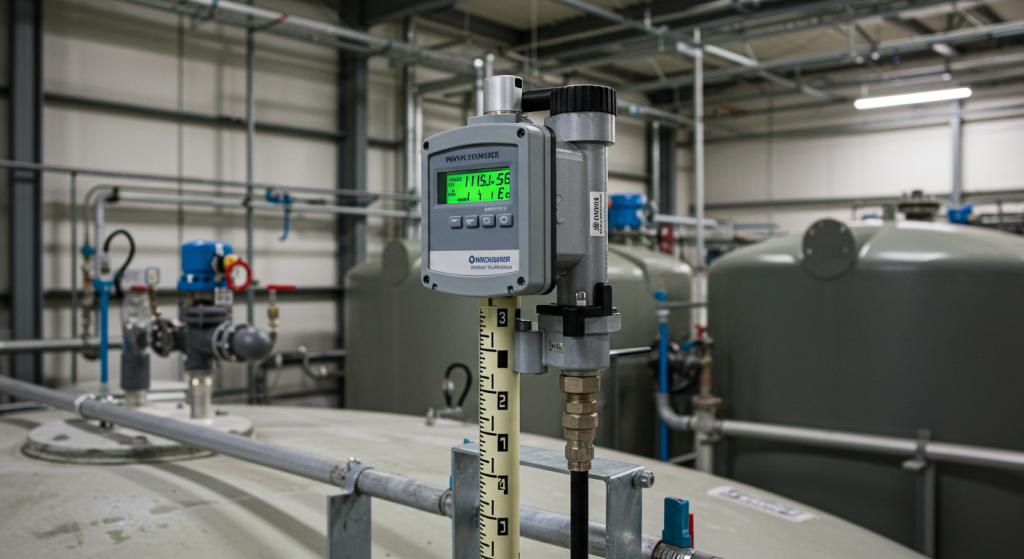
In this guide, we will explore what industrial water level sensors are, how they work, where they are used, their different types, benefits, and even the future of this important technology. This in-depth explanation is written in simple language so that even a student in 6th grade can understand it, while still providing detailed and accurate information.
What Is an Industrial Water Level Sensor?
An industrial water level sensor is a device used to measure how much water is in a tank, container, reservoir, or system. Unlike simple tools used at home, industrial sensors are designed for large operations. They can measure hundreds or even thousands of liters or gallons of water accurately and continuously.
These sensors can show the water level on a screen, turn water pumps on or off, send alerts when the level is too high or too low, and even connect to the internet for remote monitoring. This helps industries save water, energy, and time.
Why Industries Need Water Level Sensors
Industries use water for many reasons:
- Cooling machinery
- Washing products
- Mixing chemicals
- Creating steam for power
- Watering crops
- Cleaning floors or systems
Knowing how much water is available and controlling its flow is very important. If water runs out, it can stop the entire system. If a tank overflows, it can damage machines or waste water. That’s why sensors are used. They help:
- Prevent Overflows: By turning off the water supply when the tank is full.
- Avoid Dry Runs: By warning when water is low or stopping pumps.
- Control Pumps: By starting or stopping pumps based on water level.
- Automate Systems: By working with software to make smart decisions.
- Reduce Human Error: No need for manual checking or guessing.
How Do Water Level Sensors Work?
Water level sensors detect water using one of several physical principles. Each type of sensor works in a different way, but the goal is the same: to tell how much water is in a container.
Here are the most common methods:
એ. Float-Based Sensors
- A float sits on top of the water.
- As the water level rises or falls, the float moves.
- This movement triggers a switch or moves a dial.
B. Pressure Sensors
- Installed at the bottom of the tank.
- Measures how much pressure is created by the water above.
- More pressure = more water.
C. Ultrasonic Sensors
- Placed at the top of the tank.
- Sends sound waves downward.
- Measures how long the sound takes to bounce off the water surface.
- Longer time = lower water level.
D. Radar Sensors
- Similar to ultrasonic but uses radio waves instead of sound.
- More accurate in fog, steam, or foam.
E. Capacitive Sensors
- Placed along the tank wall.
- Measures changes in electric charge caused by water.
- Can detect exact levels in clean water.
Types of Water Level Sensors Used in Industry
There are many sensor types, each useful in different situations:
- Point Level Sensors
- Detect only specific points (full, half, empty).
- Common in float or switch types.
- Continuous Level Sensors
- Measure the exact level from empty to full.
- Used with digital displays and controllers.
- Contact Sensors
- Touch the water directly.
- Examples: Float, probe, capacitive sensors.
- Non-Contact Sensors
- Never touch the water.
- Use radar or ultrasonic waves.
- Good for dirty, hot, or dangerous water.
Where Are They Used?
These sensors are used in many places:
- Water Treatment Plants: To manage clean and dirty water.
- Farms and Irrigation: To monitor water for crops.
- Factories: For cooling machines or making products.
- Power Plants: To control steam and cooling water.
- Food Processing: To clean and mix ingredients.
- Buildings and Hotels: To check tank water for guests.
What Happens When Sensors Are Not Used?
Without a water level sensor, industries face big risks:
- Water overflows and damages floors or machines.
- Pumps burn out by running with no water.
- Entire systems shut down due to low water.
- Workers waste time checking tanks manually.
- Water is wasted, which costs money and hurts the environment.
Sensors are not just helpful. In many industries, they are required by safety rules.
Benefits of Using Industrial Water Level Sensors
- Saves Water: No overflows or leaks.
- Saves Energy: Pumps only run when needed.
- Saves Time: No need to check tanks by hand.
- Increases Safety: No damage from flooding or overheating.
- Better Planning: Helps track how much water is used every day.
- Remote Monitoring: View water levels on a phone or computer.
Modern Features and Smart Sensors
New sensors have amazing features:
- Wireless Connections: Use Bluetooth or Wi-Fi.
- App Alerts: Send text messages or app notifications.
- Cloud Monitoring: Store data on the internet for later use.
- Solar Power: Run on solar panels in remote areas.
- Automatic Data Logging: Keep records for safety or government reports.
Real-Life Example
Imagine a dairy farm with four big tanks of water. These tanks are used for cleaning, feeding, and mixing cow feed. Without sensors, a worker checks each tank five times a day.
Then the farm installs industrial water level sensors. Now the system:
- Shows water levels on a control panel.
- Turns the pump on or off automatically.
- Sends an alert to the farmer’s phone when water is low.
The farmer saves time, prevents waste, and always knows how much water is available. Productivity increases, and the cows are always cared for.
Challenges and Solutions
Sensors are very useful, but they must be used correctly. Challenges include:
- Dirty Water: Can block sensors. Use non-contact sensors or clean regularly.
- Temperature Changes: Some sensors need protection from heat or cold.
- Power Cuts: Use battery or solar backups.
- Wrong Placement: Must install at the correct height and angle.
With proper care and smart choices, these problems are easy to solve.
Future of Industrial Water Sensors
Sensors are getting smarter every year. In the future:
- Sensors will use AI to learn and predict water use.
- Tiny sensors will be placed inside pipes to measure flow.
- Systems will talk to each other to adjust water use in real-time.
- Sensors will be cheaper and used in every factory and farm.
These changes will help save water and protect the planet.
નિષ્કર્ષ
An industrial water level sensor is more than a tool. It’s a smart helper that watches water so people can focus on other work. It helps save water, money, time, અને ઊર્જા. It protects machines and makes workplaces safer.
From simple float sensors to high-tech radar systems, these sensors are used all over the world in industries big and small. Understanding how they work and why they matter is the first step to using water wisely and working smarter.
Whether you’re a student, a teacher, or someone working in industry, learning about water level sensors opens the door to technology, science, and sustainability.